
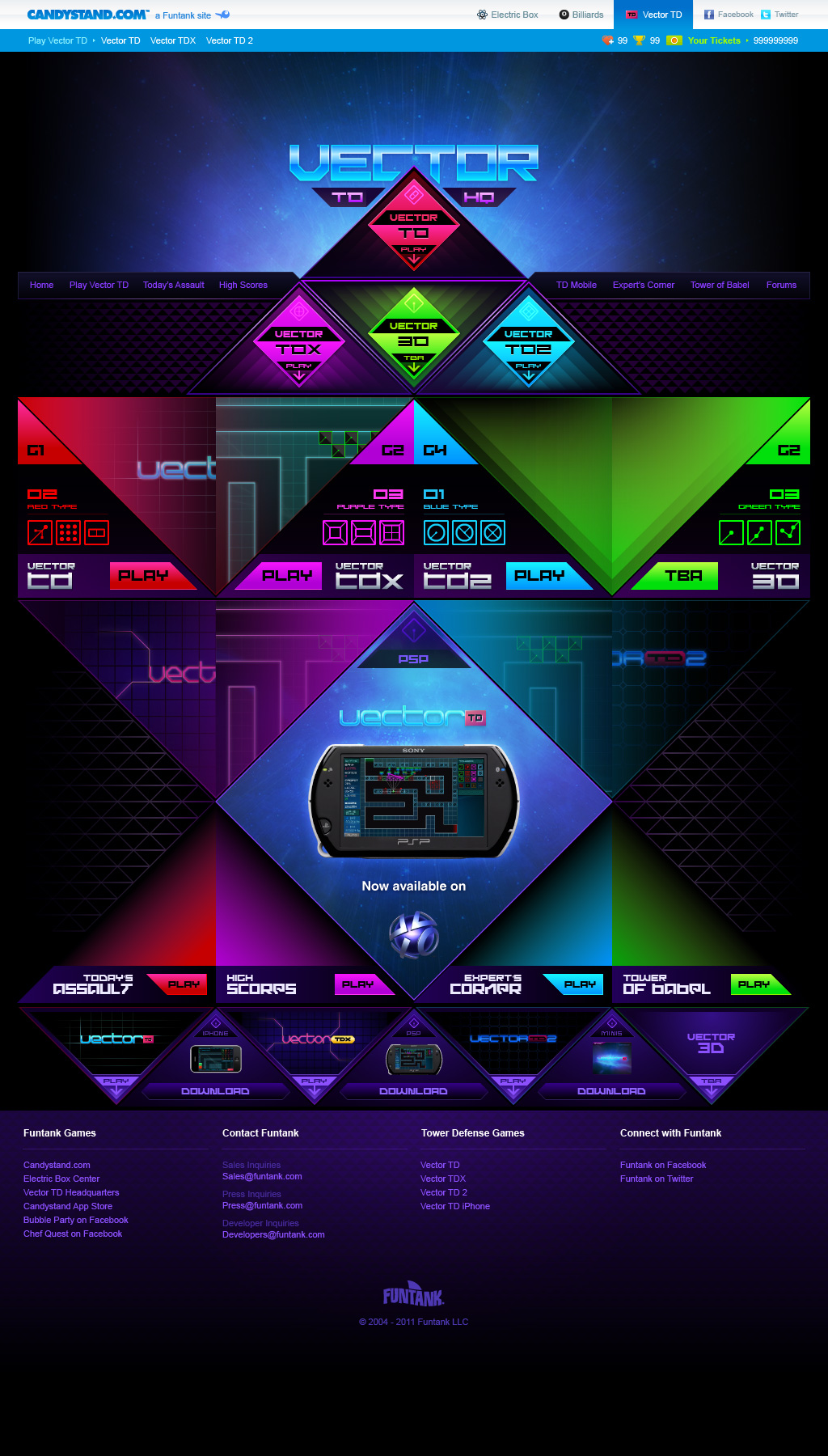
If someone has some insight on this it would definitely help with an ongoing project From my understanding and research, this capability is not available in the HAAS NGC post. We want to move to an X and Y have the spindle going and have to part rotate. So we have been planning to use our rotary table vertically in the Z axis. Currently have a part that is outside the X and Y travel of our HAAS VF2. Lots of different ways of doing the job, this has been just one offering, the OP doesn`t say whether he starts off with a Casting or an already roughed out or a solid block that needs some roughing out but it can all be done (carefully) with some thought
VECTOR TD GUIDE AROUND TH CODE
Just have to do a little Math to get the C axis rotation feed to match the Z axis feed for optimum cutting or even just set the C axis running and then lower the Z axis using the Jog or a hand held MPG would be easy as well, X axis can be used as well to size the ring accurately, not everything has to be done with Code In a way it is using the Mill as a Vertical Borer when the diameter of the job exceeds for example the (Usually) shorter travel of the Y axis.
VECTOR TD GUIDE AROUND TH MANUAL
Yes, a constant rotation of the C axis while machining from above is exactly what the OP wants to do, in other words the X and Y do not move and the Spindle runs and slowly moves down in the Z as the C axis turns.Ĭommon practice back in the day with old Manual turntables when it wasn`t possible to cover all of the table with the machines X and Y axis because the job was too big, do an operation at one point of the X axis then move to the next area, or to do something like the OPs ring just set the Z axis to moving down slowly and then turn the handle to rotate the turntable as the Z axis decends !! Hopefully someone else will come up with a much better solution for you, this is an odd is only a theory and would only work if the CNC Control will allow it. Painful way to do it in sections but you might be able to do it all in one go with the right tooling I didn`t know whether you are using inches or mm so I just set the feed to F20 but you can set that to whatever. This may be completely useless but might point you in the direction you want to go ! ! Will have to be creative with your tooling, there is an undercut where you would need touse something like a Slot Cutter/Slitting Cutter to get under it but you can do something like my original idea by using say the 3D Contour that will in effect "Ramp Down" as the C axis rotates, a rough/crude way to have the C axis running might be to again do a Manual NC "Passthrough" that is inserted at the begining as in th file attached, work out the number of rovolutions you get in the toolpath, say for example 20, x that by 360 and put the 7200 value in a Manual NC as in the image below, just a theory and your machine control may not allow the number of rotations, may need a Parameter changing.
